TBK Automatisierung und Messtechnik GmbH in Graz, Österreich, ist das Kompetenzzentrum für Laser-Messeinrichtungen und eine 100-prozentige Tochtergesellschaft der SMS group.
Unternehmen
Kundenspezifische messtechnische Lösungen für Langprodukte
Die TBK Automatisierung und Messtechnik GmbH entwickelt seit 1986 messtechnische Lösungen für die Stahlindustrie, insbesondere Lasermesssysteme auf Grundlage des Lichtschnitt-Verfahrens. Seit 2004 arbeiten die beiden Unternehmen, TBK und SMS group, eng zusammen.
TBK bietet für den Bereich der Langproduktanlagen maßgeschneiderte Lösungen zur Dimensionskontrolle und Oberflächenanalyse von Walzprodukten an – z.B. von Draht, Stabstahl, Profilen und Schienen sowie Rohren, aber auch von Halbzeugen, wie stranggegossenen Knüppeln oder Vorblöcken.
Einrichtungen zur Messung der Geradheit, insbesondere für Schienen, und Messgeräte für Sonderprofile und Räder ergänzen das Produktspektrum.
Technologie
Hohe Abtastraten, kurze Belichtungszeiten sowie absolute Synchronität sind die wesentlichen Merkmale, durch die sich TBK Sensoren von anderen Lichtschnitt-Sensoren am Markt unterscheiden.
Mit dem von TBK eingesetzten Lichtschnitt-Verfahren kann die gesamte Kontur des Produkts unabhängig von seiner Form geprüft werden.
Die von TBK entwickelten Sensoren messen bis zu 15.000 Konturen pro Sekunde. Dem Prinzip der zweidimensionalen Triangulation folgend, wird eine Laserlinie auf die Produktoberfläche projiziert. Diffus reflektiertes Licht liefert die Basis für die Erfassung von Querschnitten, aus welchen relevante Informationen zur Steuerung des Walzprozesses generiert werden können.
Die TBK Systeme sind in der Lage, unter Verwendung dieser Werte, den genauen Querschnitt des Produkts zu berechnen. Mit der hohen Auflösung und hohen Messdichte kann ein 3D-Modell des Produkts generiert werden, das auch Oberflächenfehler erkennt.
Systematische Qualitätsverbesserung auf der Basis von Messdaten
Auf der Grundlage der hochpräzisen Querschnittsmessungen erzeugen TBK Systeme genaue Informationen, die für die Steuerung des Walzprozesses wichtig sind, und laden diese zurück in das Produktionssystem. Je nach Anlagenlayout werden die Modelle an den Arbeitsstationen der Anlagenbediener angezeigt oder automatisch von den Steuerungen der SMS group analysiert, um die Produktqualität und die Anlageneffizienz zu steigern.
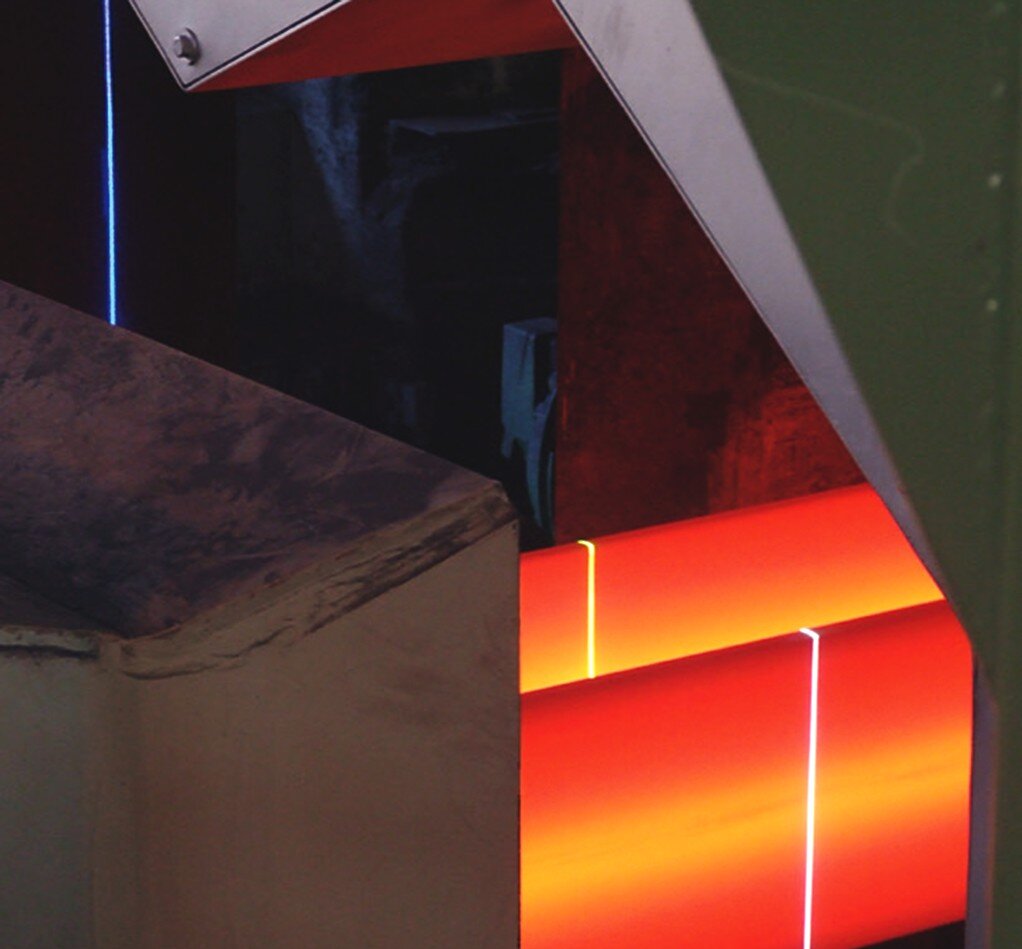
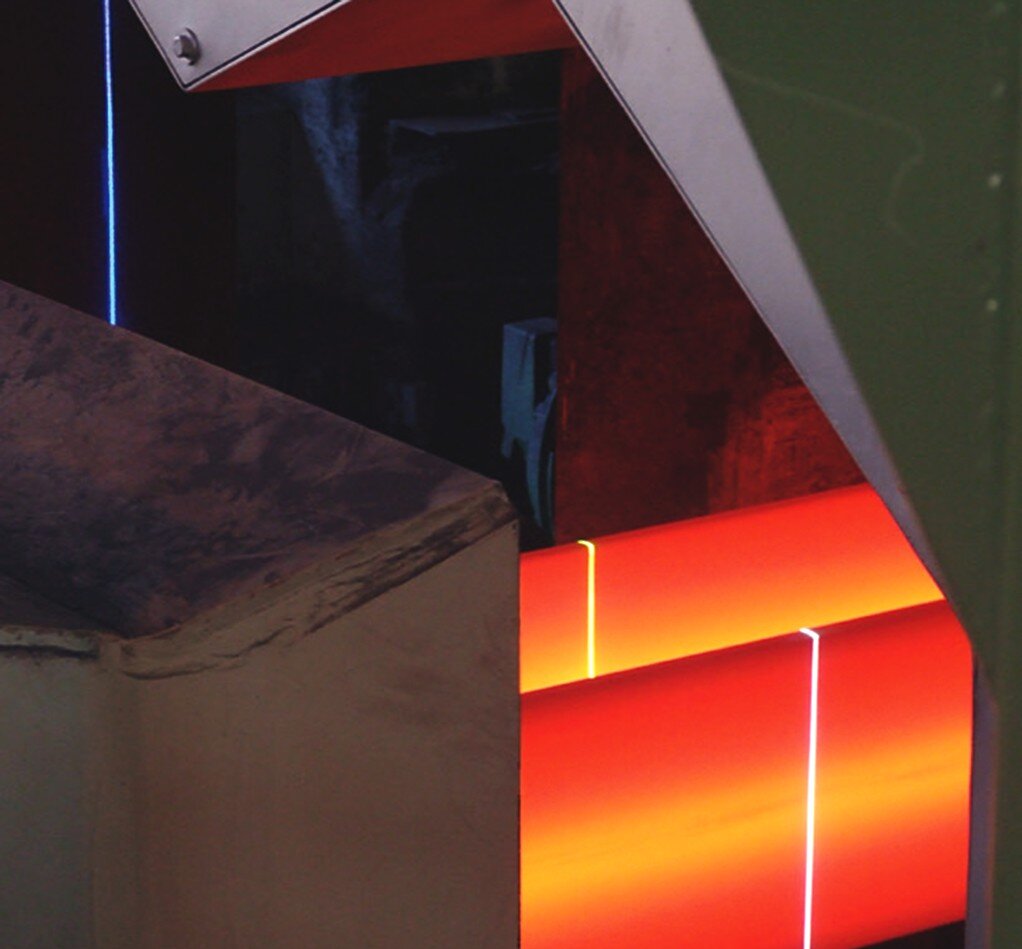
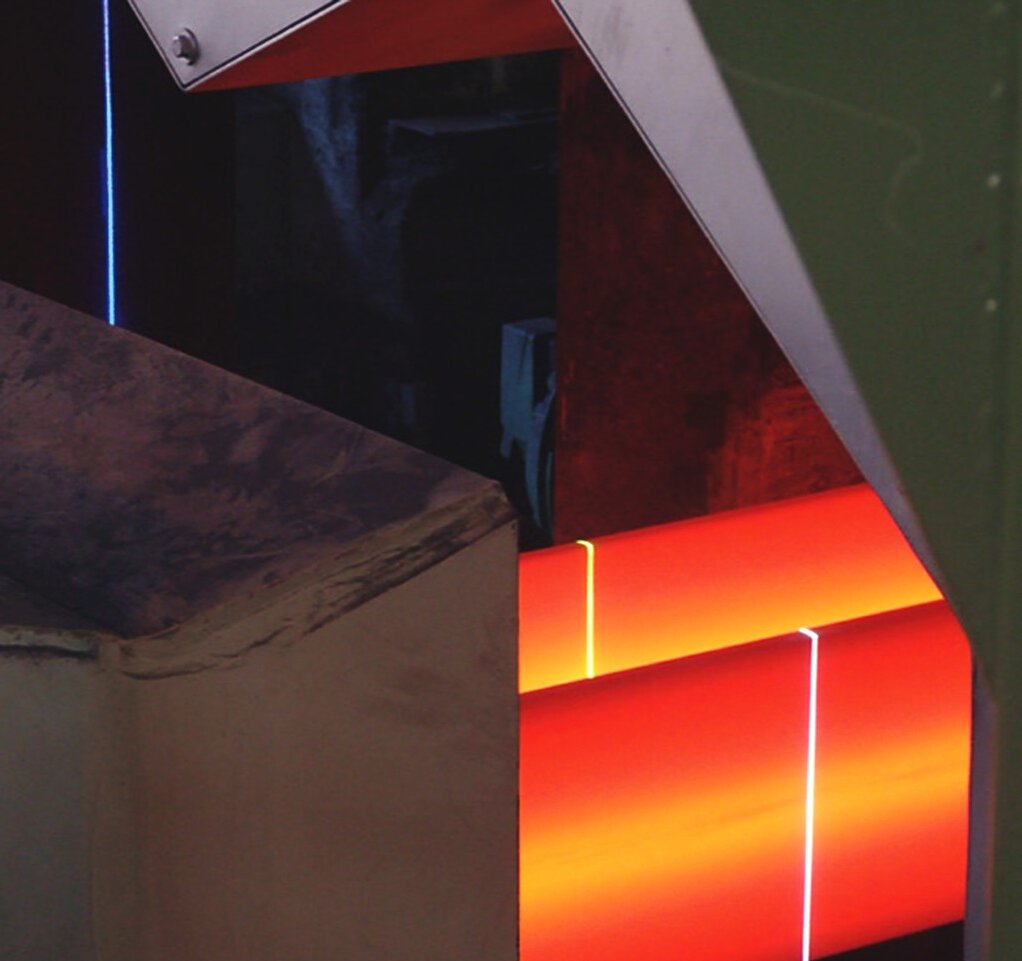
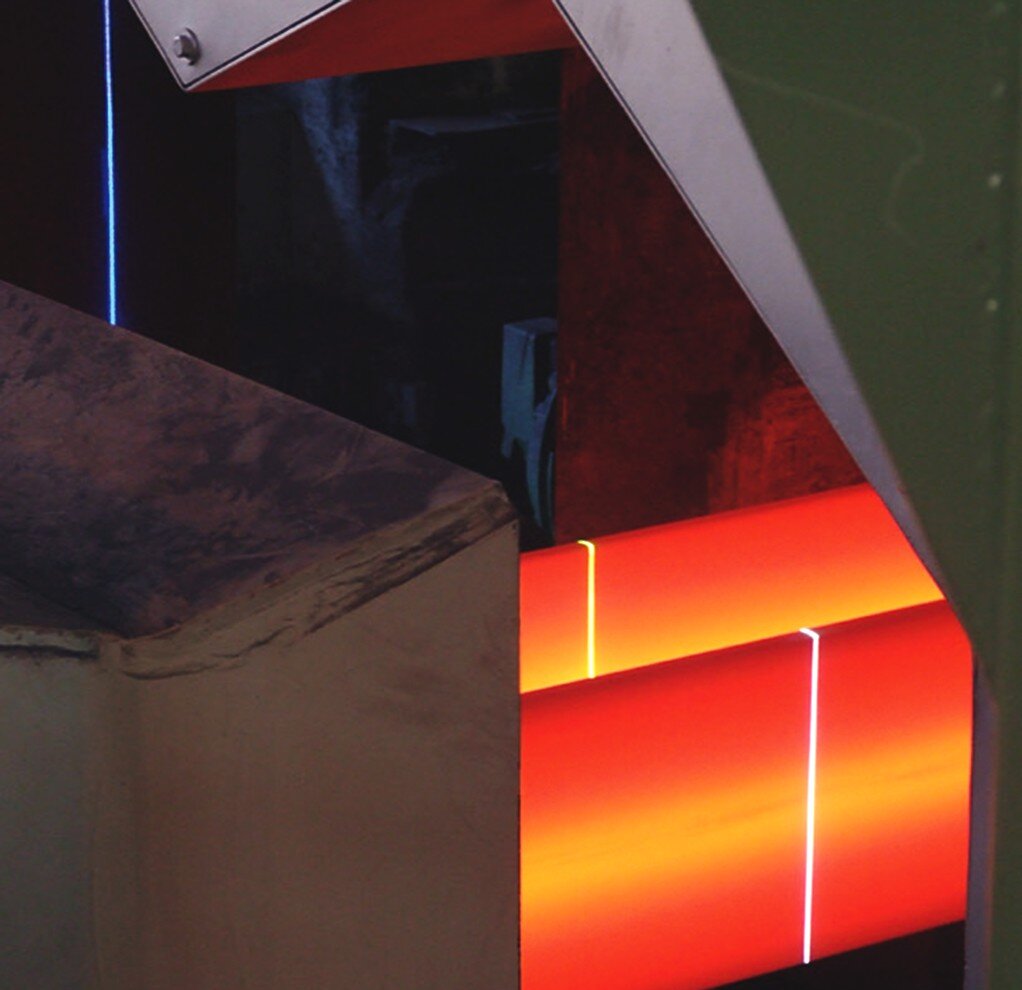
Lösungen
Kompetenzen und Produkte
TBK Systeme können für das gesamte Spektrum von Langprodukten einschließlich Draht, Stabstahl, Rohre, Profile und Schienen sowie Sonderprofile als auch für stranggegossene Knüppel und Vorblöcke eingesetzt werden. Unser Portfolio deckt auch die Vermessung von gewalzten Rädern oder Ringen sowie Schmiedeprodukten ab.
Highlights
Die automatische Sammlung von Produktdaten ist essentiell für die Digitalisierung
Einschlägige Schlüsselwerte aus erprobten Algorithmen
Gewöhnlich sind es Anlagenbetreiber, die Entscheidungen in Bezug auf die Produktionssteuerung treffen; relevante und präzise Leistungswerte liefern hierfür eine sichere Grundlage. Zusätzlich zu den normalen bekannten Werten liefern TBK Messeinrichtungen ein breites produktspezifisches Spektrum an Dimensionsparametern. Erprobte Algorithmen, die sich als leistungsfähig erwiesen haben, werden genutzt, um Leistungswerte aus den gemessenen Konturdaten zu erzeugen.
Walzwerk Industrie 4.0
Ziel ist es, einen stabilen Walzstraßenbetrieb mit hoher Auslastung sowie eine durchgängige Produktqualität aufrecht zu erhalten. Ein vollautomatisches System zur Produktionssteuerung und Datenerfassung ist grundlegend für die Digitalisierung. Darüber hinaus sind Prozessdaten bzw. Produktionsdaten zusätzlich zu Daten des Produktzustands erforderlich, um den Prozess an die verschiedenen Bedingungen anzupassen. TBK Messsysteme sammeln Daten über den Zustand des fertigen Produkts einschließlich seiner Geometrie, Form sowie Abmessungen und Oberflächenzustände ebenso wie Daten über Temperatur und Walzgeschwindigkeit.
Kontakt
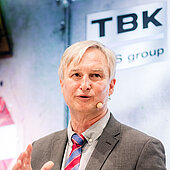
Ralf Kremer
TBK Automatisierung und Messtechnik GmbH
Schmiedlstraße 8
8042 Graz
Austria
Telefon
: +43 316 405574 13

Gernot Scheiflinger
TBK Automatisierung und Messtechnik GmbH
Schmiedlstraße 8
8042 Graz
Austria
Telefon
: +43 316 405574 34
TBK Automatisierung
und Messtechnik GmbH
Schmiedlstraße 8
8042 Graz, Österreich
T +43 316 405574 0
F +43 316 405574 2
office@tbkautomatisierung.at
www.tbkautomatisierung.at
Firmenbuchnummer:
FN 250894 m
Registergericht: Graz
USt.-Id. Nr.: ATU58116746